Go behind the scenes of the record pressing business in our in-depth interview with President & CEO of Furnace Record Pressing, Eric Astor
Furnace Record Pressing in Alexandria, VA is no newcomer to the vinyl game. Their owner has been in the business for 30 years, and they’ve been in the record pressing game since the mid-90s. Now, with an expanded 50,000 square foot facility and a thriving consumer base eager for new wax, it looks like the best days may just be ahead for Furnace and its crew. We recently sat down with President and CEO Eric Astor to discuss his company, the current state of the vinyl resurgence and where he sees things headed in the future.
Can we start with how the whole Furnace business came into being?
Well, I’ve been in the music industry since I was about 14 or 15, playing in bands and doing fanzines. I started by putting out 7-inches by local bands and friends’ bands. I grew up in Tempe, right outside of Phoenix, where there wasn’t a lot to do back then. I was out in the suburbs, so you kind of had to make your own fun.
Since ’86 or so, I’ve been getting records recorded, mastered and cut. I was putting lacquers on the back of a scooter and running them over to the pressing plant. After I had a second record label once I moved out the East Coast – this was all punk rock and indie stuff – we were having a hard time distributing our products. So, we decided to handle our own distribution, as well. We started a distribution company called Lumberjack, which was mainly set up to get a bunch of record labels about our size that were in the same boat as we were, having a hard time distributing and getting paid. It was a strength in numbers things, and we quickly found out a lot of these labels were having trouble getting things manufactured, too. We started helping out by getting things press ready and print ready for these labels.
It turned out that I loved the manufacturing side of it more than distribution, so in 1996 I started a separate company, which was Furnace, and we’ve been in business ever since.
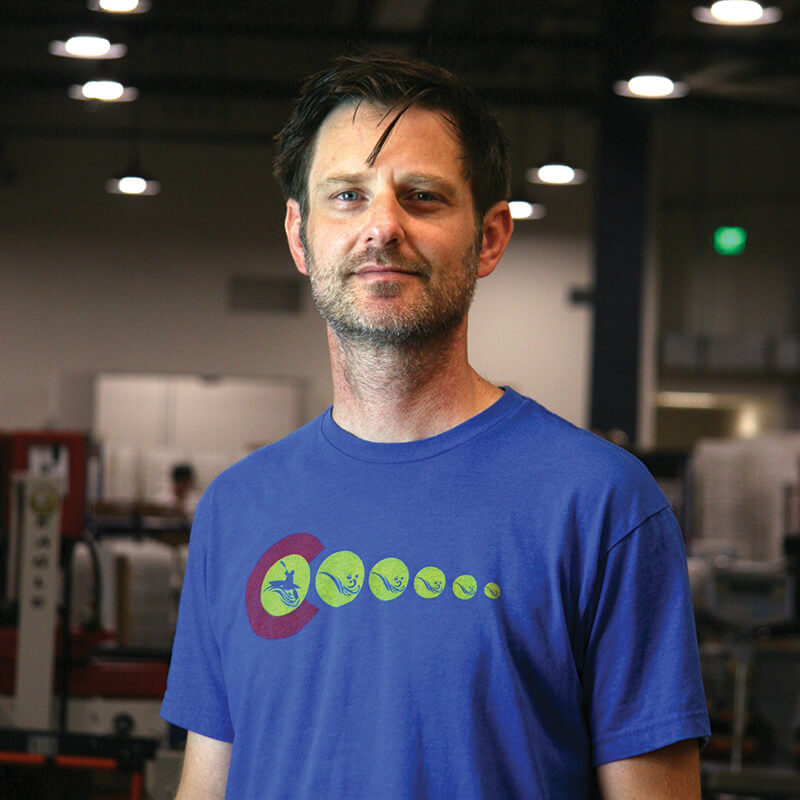
Eric Astor
So, were you pressing vinyl at that point, or working with labels to broker pressing?
When we first started, we were brokering vinyl and that quickly went away when CDs and DVDs took over. And about 10 years ago, these companies came to me and said they liked how we handled all their weird releases, and approached us for [vinyl]. So, I reached out to Pallas in Germany who was really well known for quality reissues – at the time there were only three plants in the world where people went for quality records. And I think because they were far away and maybe didn’t have the best English skills, they weren’t all booked up [by US labels]. We basically badgered them into working with us, and they didn’t have a whole lot of work to do since the European vinyl renaissance hadn’t really happened yet, so within three months we filled an entire first shift at their plant and became their biggest customer.
In time, we started building our own presses over there. We had five presses over there, and would bring vinyl back to the States. But about three or four years ago, we saw the demand for vinyl change a lot here. A lot more people were interested in colored vinyl, shorter runs, not as many 180-gram [releases]. That wasn’t our strong suit in Europe, which is when we started to look for equipment and space to expand what we had [here].
Unlike a lot of brokers, we were bringing sleeves back from Europe, and doing all the assembly and shipping from our location, whereas most companies were bringing in finished goods.
So, it was time to start pressing things yourself here. Where do you even start looking for equipment?
We found some Swedish machines down in Mexico that were in good shape, so we bought those. But we had to find someone in England to refurbish them, which took a long time. After we started doing that, a few companies started making new presses, so we found that we had people making spare parts for the old machines along with the new. Obviously, if we had started this a little later, we would have brought in all new machines, since the old ones are a pain in the ass!
How long did it take to plan out the new facility?
It took about three years to get everything conceptualized, rehab all the equipment and map out the facility. It’s not like there’s a template in place, or someone you can go to who’s built a pressing plant before to get a set of blueprints. It’s all very specialized, which took a lot longer and was very expensive.
We built up a team with people who’ve been in the pressing world for a long time, so we were able to go from starting up the presses and getting records done in about two days, as opposed to months. We’re still figuring it out, but we have a laser-focus on quality, making sure we’re pressing great records. Not just churning out volume and hoping for the best.
From the operations side of things, do you find there’s an interest in people wanting to come on board and learn these specialized skills? I would imaging it’s a big concern to have people who understand these machines in the years to come…
Sure, this isn’t easy work to do. Successful press operators have to know hydraulics, air, steam, cold water chillers and boilers…what we’re making a conscious effort to do is bring in people who’ve worked in our other areas to teach them this process. People are interested in seeing how it’s done, so we have people from all different backgrounds learning how these things are handled.
The old timers who’ve been in the industry for a long time, they’d love to retire. So, we’re trying to download all their experiences and know-how to create the next generation of people to press good records and who can maintain and fix these machines. A lot of that just comes with experience; it’s not something you can read from a book.
Let’s switch back to bands – obviously there’s a lot of renewed interest there in pressing records. What advice can you give to artists looking to get into vinyl for the first time?
The biggest piece of advice is before you even record, talk to the person who’s going to cut the lacquer for your record. There are very, very few people who do this. There’s an art and science to that process – the biggest thing we find is that bands go into the recording studio, and record things that are hard to transfer to vinyl.
You can only fit so much music on a record, and you have to take into account the physics of how a record plays back, since the inner grooves of the record play differently from the outer grooves. If you look back, bands used to have a plan. They’d go into the studio and sequence [albums] based on putting the louder songs toward the beginning of the side, and the softer side towards the end of the side. On the outside grooves, it’s still spinning at the same speed, but covering a lot more area. So those outer grooves are going to play back better and louder; there’s just more information there.
Where in the process does the lacquer cutting occur? Is that before the band approaches the you, the pressing plant?
You generally go into a pre-mastering or final mastering stage where you get all the EQ settings right where you want them, then you’ll either have the lacquer cut then, or that might be a separate process handled by another company. If you’re new to the process, we can help assist you with all of that. You can come to us with the master recording, and we can help you handle everything from the time the master’s done to the final artwork and pressing.
It all comes down to knowing what you can fit on the record, and getting the sequencing right. Be prepared before you get into the process.
You guys are trying to do this in the most environmentally sound way possible, too. Can you touch on that aspect of the business?
I’m a big tree-hugger, I spend a lot of time outside. We’re in an industry that can be dirty — we’re using gas, electricity, plastic and paper. If you do it right, you have a lot of quality control so you might typically end up throwing away [materials]. For us, about 90% of the discarded plastic/PVC can be reground and recycled, and we also heavily recycle cardboard and paper.
We have a closed-loop system for heating and cooling and chilling, so it decreases the amount of water we use. We’ve built up redundant systems that allow us to use fewer resources, and we’ve even put in check valves and systems on our boiler so we’re able to step down the boiler when we’re not using all the presses, in order to reduce the amount of steam we’re using at any one time.
We’re trying to do a lot of things like that. In the long run, it saves you money as well. It’s all about not creating waste and as it happens, it helps the environment too. When we start making a profit [laughs], we’re also going to be donating 5% of our profits to environmental causes that will help negate our carbon footprint, plant more trees and eventually when you order from us, it’ll show you what your carbon footprint is for your order, what we’re doing to negate that and we’ll offer the customer an opportunity to donate as well to help bring that down even further.